Peak Spray Foam Insulation's SHOWCASES
Air Barrier & Insulation at Cold Spring Fire & Rescue
Our crew spent nine days in Cold Spring, MN, working on the new Cold Spring Fire & Rescue building. We began by sealing all openings, corners, and transitions with weather barrier detail flashing. Then, our spray foam technicians installed R-14 Icynene® HFO Max closed-cell spray foam across the entire exterior brick, providing air barrier protection, weatherproofing, and insulation. Spring weather in Minnesota brought its challenges, but one of our biggest considerations was the building’s location along a busy downtown street. With regular traffic and nearby parked vehicles, we took extra care to manage overspray and ensure a safe, clean application while staying on schedule.
custom HOme insulation with bronder construction
We meticulously installed R-21 closed cell foam in the walls of the main and second floors, as well as in the garage walls and rims. For enhanced insulation, R-30 closed cell foam was applied to the cantilevered sections of the main floor and the slanted areas of the storage room. Additionally, we applied a DC315 coating over the spray foam in the four-season porch walls for added protection. To ensure optimal airflow, air chutes were installed in the eaves of the garage, house, and second-floor bonus room slants. We then used R-50 loose-fill blown fiberglass and 6-mil Duraskim in the main floor vaults, garage ceiling, master bedroom, and bonus room ceiling. For the second-floor non-vaulted ceilings, we applied R-50 loose-fill blown fiberglass and 4-mil poly.
We also sealed all openings and penetrations with can-foam and installed R-11 sound batts in the walls of the main and second floors. For superior soundproofing, we added 18 inches of loose-fill blown fiberglass with netting on the main floor truss assembly. Finally, a comprehensive Blower Door Test and Report will be conducted to verify the home’s energy efficiency.
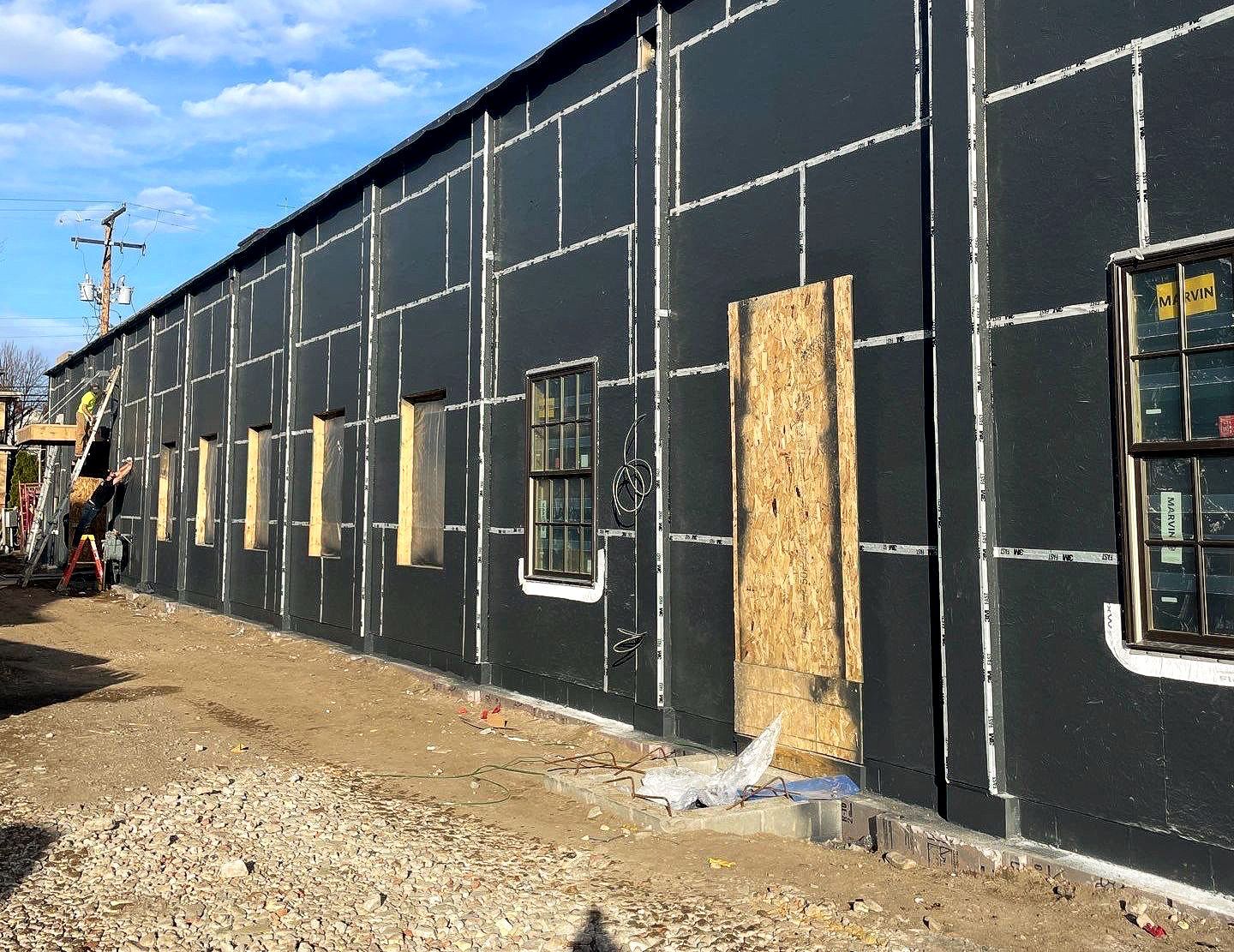
all saints church foam & weather barrier installation
For this project, we installed R-21 closed cell foam insulation in the exterior walls to provide thermal protection and improve energy efficiency. In the vestibule cantilevers, we used R-30 closed cell foam to ensure superior insulation and comfort in these high-impact areas. Additionally, we applied Hydromax above-grade weather barrier over the plywood on the exterior walls to offer enhanced protection against the elements, ensuring long-lasting durability and resistance to weather-related damage.
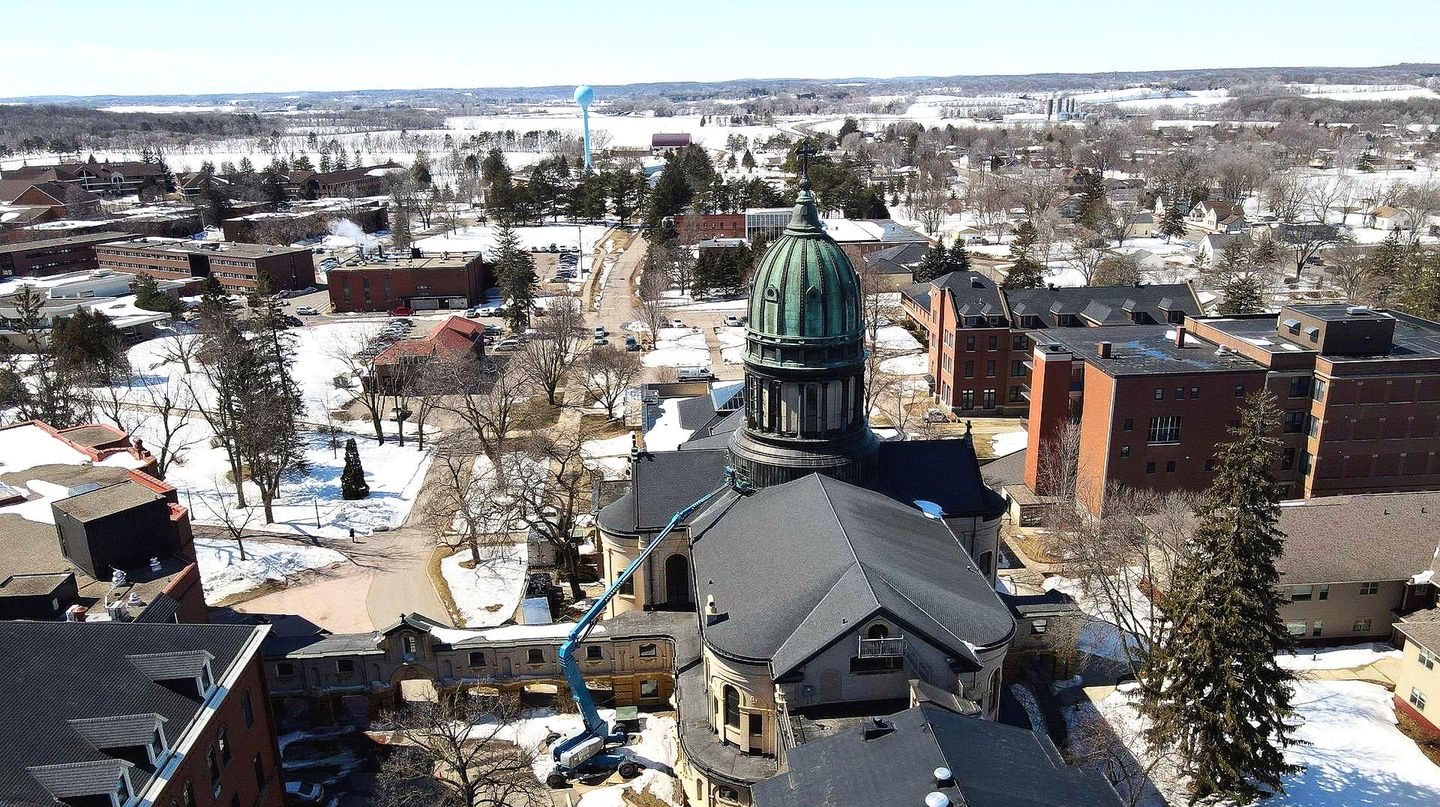
Sacred Heart Chapel attic reconstruction
We undertook a significant ceiling and attic reconstruction project at the historic Sacred Heart Chapel in St. Joseph, Minnesota, utilizing 29,000 board feet of material to establish a robust vapor barrier within its iconic dome. Given the chapel's 112-year-old heritage, our solution involved applying 5.5 inches of spray foam to achieve an R-value of 38, followed by a DC-315 thermal barrier coating for added protection against condensation.
Working 135 feet above the ground, we prioritized safety with comprehensive harnessing and lift operation training for our team. The challenge of mobilizing equipment was met with innovation; we carefully maneuvered 270-foot hoses up the dome by securing them with ropes and straps at anchor points, allowing us to work efficiently. The spray foam installation proved to be the optimal solution for addressing the building's moisture issues, significantly reducing the need for future remediation and structural repairs. This approach not only enhanced the chapel's energy efficiency but also preserved valuable resources and materials.
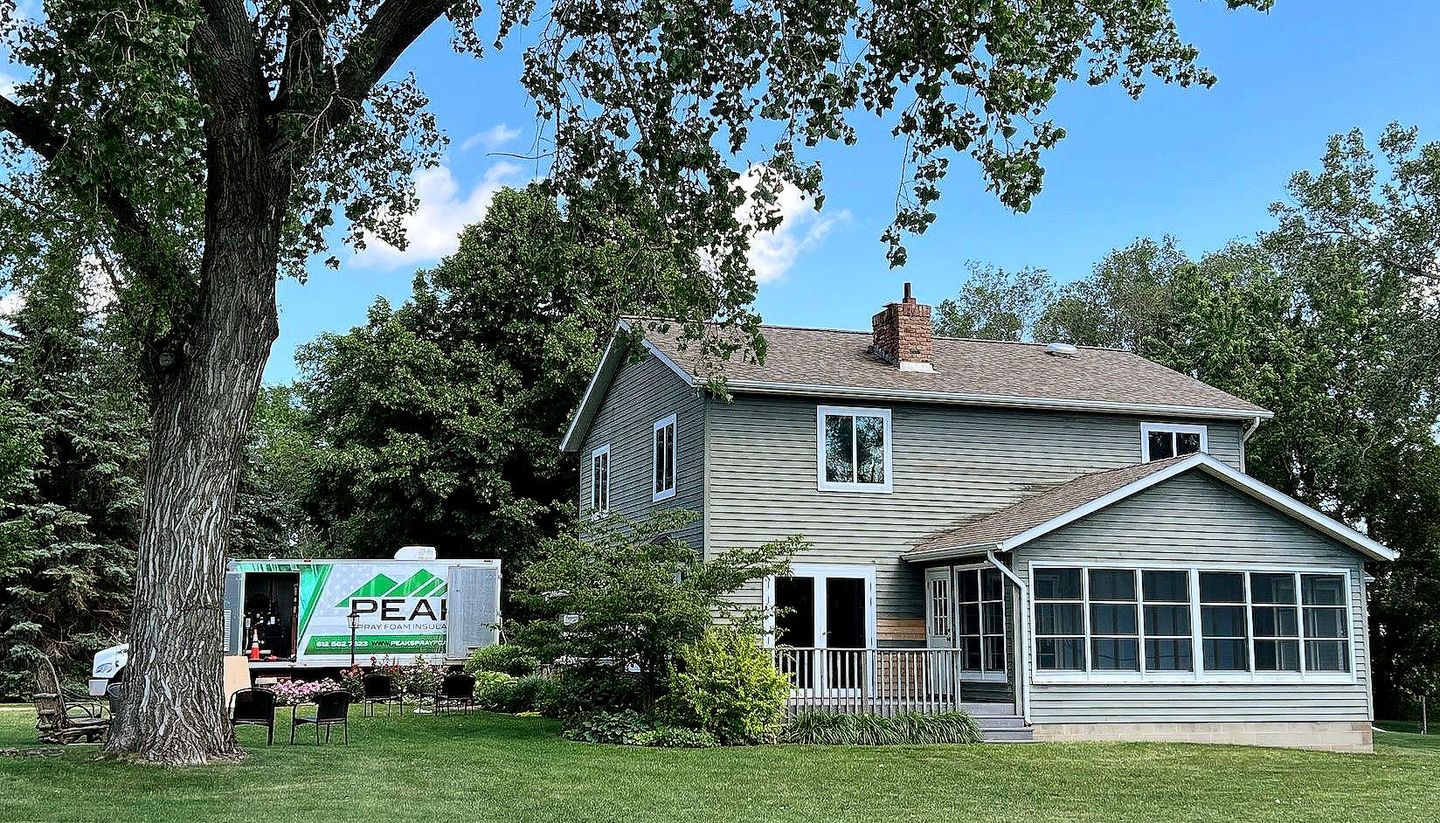
Stowman Home renovation
Mr. Stowman wanted to create a legacy home for his two adult daughters who struggle with multiple health issues and chemical hypersensitivities. Their single-family home was experiencing significant indoor air quality issues and hypersensitivity challenges for the building occupants. A detailed analysis was conducted which identified sources of mold contamination, as well as the root cause related to building deficiencies. As part of the remediation program, Peak removed the old fiberglass and kit foam from three attic areas. Dimple board was installed to promote drying in the basement, but off gassing from the newly installed drain mat triggered severe reactions with the young ladies. To fix the problem, the Stowman family decided to have Ultra-Pure® HD closed cell spray foam installed in all the exterior building envelope walls and attic spaces as a means of both addressing insulation/moisture management requirements as well as mitigating or minimizing chemical sensitivity challenges that arose from new products being installed. To meet the stringent indoor air quality requirements for the hypersensitive daughters, Ultra-Pure™ HD closed cell system was selected, providing exceptionally low VOC and low odor footprint in addition to high performance insulation of Ultra-Pure™ Low VOC SF. This was the first time Peak, or their suppliers had a client with sensitivity issues related to newly installed materials during a restoration project. Therefore, using extreme caution and good communications with homeowner, Peak took extra steps in the material selection process to introduce low VOC spray foam in small quantities to ensure compatibility. Additionally, the strict ventilation process along with documented VOC monitoring before, during, and after the installation validated the near baseline impact of these products, resulting in full compatibility with the hypersensitive daughters. Sharing product information, material selection samples and on-site monitoring resulted in a very satisfied homeowner, pleased with his choice of insulation and the discipline Peak followed during installation. As a follow-up, the family was impressed with the insultation performance during the first cold snap, no more drafts from frigid prairie winds!